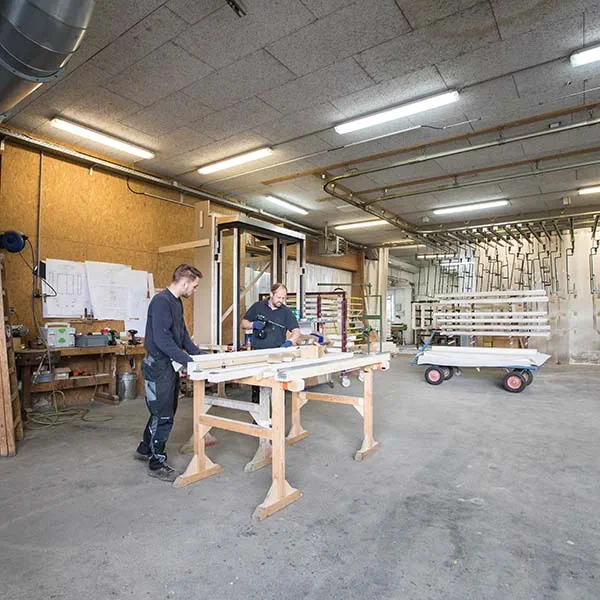
Perfection down to the last screw
A project with 45.000 screws. In the starring role: The T 18 cordless drill from Festool.
What do the German Bundestag, AIDA cruise ships and the University of Southampton have in common? It's perfectly simple: As soon as high-quality woodworking came into play in one of these projects, the timber construction company VHB got involved.
Georg Rothärmel, Head of the Workshop at Vereinigte Holzbaubetriebe (VHB), welcomes us at the entrance to the production hall at just before eight o'clock. His jumper proudly displays the orange VHB logo. A few sawing chips testify to the practical nature of his job, even though he himself only rarely picks up tools these days. "Some days, that can be quite hard," he reveals and laughs while we are walking towards his production area. On the way, he takes the time to remind us of the most important key facts about the company: VHB employs 125 members of staff in total. The company grew from the merger of two timber construction companies in the 1970s. That was over 40 years ago now. In 2015, the company recorded a turnover of €23.9 million – by no means a small achievement. VHB specialises in high-quality constructions and extensions for interior and exterior areas. Even cruise ships, for which VHB mainly finishes pool areas with wooden elements, make a regular appearance in the order books. The company also constructs wood-glass façades and wood-aluminium façades. The different projects are realised at three production sites with a total area of approximately 5000 square metres.
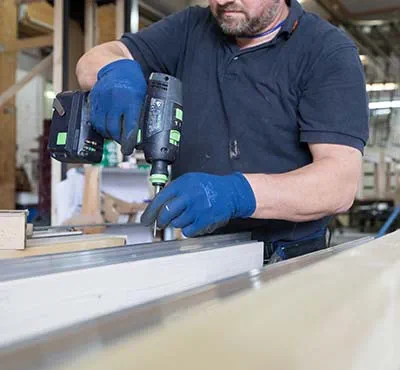
56 wooden bay windows – 45,000 screws
Two members of the assembly team are in the middle of constructing a frame. They are calm, the work is routine and goes off without a hitch. Evidently, it's not the first time that these two have assembled a wooden bay window together. The look and smell of the wood tell us that they are working with fir. "Fir has ideal properties: It contains less resin than spruce, withstands all weather conditions and, to top it off, is well suited to screwdriving," Georg Rothärmel reveals and goes on to say: "This here is a bay window we are building for a new retirement home in Schutterwald. When we are finished there will be 56 wooden bay windows – that's approximately 45,000 screws. So we do a lot of screwdriving here. We mainly rely on the T 18 cordless drill from Festool for that, because it offers an excellent compromise between light weight, versatility, endurance and robustness."
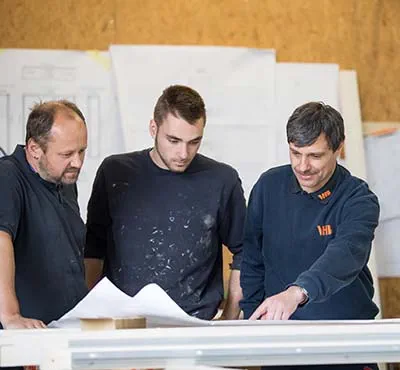
Timber construction par excellence
What follows is a short briefing with Rothärmel's team outside his office. A purely office-based job? Out of the question for Rothärmel. The experienced workshop manager is always in the thick of it and knows every project in detail. To him, communicating with his employees is the be-all and end-all. That is incredibly important, since VHB specialises in large and accordingly demanding timber construction projects. Customers include the German Bundestag and the Nordic embassies in Berlin, the Council of the European Union and the European Court of Justice in Luxembourg with an extension. "For these large projects, excellent coordination and precisely planning people, materials and machines is indispensable," Rothärmel explains. "We recently refurbished some of the wooden furniture in the Bundestag. We could only do that at night, so as to not disturb anyone with our work during regular office hours. Not the easiest task, but we always take our cue from what our customers need."
Wood in its most beautiful form
Elsewhere in the workshop, employees are sanding different wooden components for the bay windows. Here, with sunlight shining through the windows of the production hall, the almost ivory-like appearance of the fir wood really comes into its own. Besides, fir is coming back into fashion: Despite its former reputation of being hard to process, the wood is increasingly used today, not least because it can withstand almost any weather conditions. "Fir is sanded down before assembly, so that we can varnish it later on. Normally, we would use the ETS 125 eccentric sander together with the CTM 26 mobile dust extractor for sanding. But in this case, we prefer to use manual abrasives, as the removal rate with a machine would be too high," Rothärmel explains.
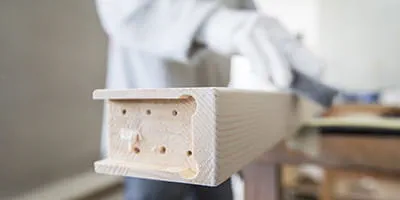
„It is very important to us that the batteries last a long time. Every time we have to change a battery it costs us valuable time, which adds up at the end of the day. That is why endurance is more important to us than just pure strength.“
Georg Rothärmel - VHB
Screwdriving around corners
The first assembly step is to screw the aluminium frame to the wood. The force applied with the screwdriver must be precisely controlled so as to not damage the sensitive frame or the wood. Fir is particularly prone to splintering in response to careless treatment. Here, the T 18 can really play to its strengths as a professional assembly tool: Using the elbow attachment, the team can easily access even the hard-to-reach areas and corners on the bay windows. They neatly drill in screw after screw – and in just under half an hour, the bay window is assembled. "Even though we have more than enough chargers, it is very important to us that the batteries last a long time. Every time we have to change a battery it costs us valuable time, which adds up at the end of the day. That is why endurance is more important to us than just pure strength," says Georg Rothärmel.
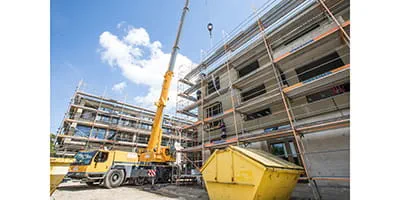
Control isn't everything
Scene change: After being assembled in Memmingen, the wooden bay windows are installed on the structure in Schutterwald. The assembly team has positioned a crane to lift them into the correct position. After just a few minutes, the crane is extended to a height of 50 metres – a diesel engine supplies the crane drive's compressor with power. Then everything happens very quickly: The first bay window is "on the hook". What looks easy at first, soon turns out to be a complex process. Some of the frames need to be lifted over the roof of the building and moved to exactly the right position on the other side, by a matter of centimetres.And because the frames are not particularly heavy, they are very susceptible to gusts of wind once airborne. But the team has everything under control: Two colleagues are stood on the roof, radioing instructions to the crane driver. "Trust is at least as important as control in these situations," the crane driver calls to us from his cab. The diesel engine is running at full power. The next window rises up into the clear blue sky. Fortunately, there is barely any wind on this morning in spring. One bay window after the other glides safely through the air to its final position.
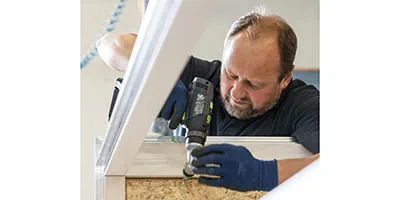
On the home stretch
On the other side of the building, two installers are already impatiently waiting for the bay windows to arrive. "It's all about precision and speed for us," one of the VHB installers tells us while his colleague is already purposefully drilling in the first screws with the Festool T 18. The frames are screwed tightly onto the steel rails protruding from the outer wall. And just like that, the bay windows are one with the building. The same is done on the ceiling. The team works together as smoothly as a pit crew during a Formula 1 race: After just five minutes, the bay window is in the perfect position – and the next window is already on its way. By late afternoon, all bay windows are installed. We ask the team how their batteries are holding up. "The batteries are absolutely fine, but we did use the larger 5.2 Ah batteries today," one of the installers responds and jokes: "As for us, we are completely drained. Tomorrow we'll be back at it with full batteries."
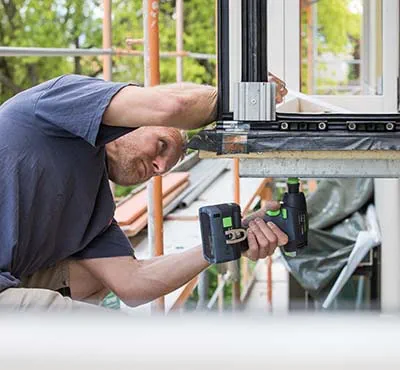
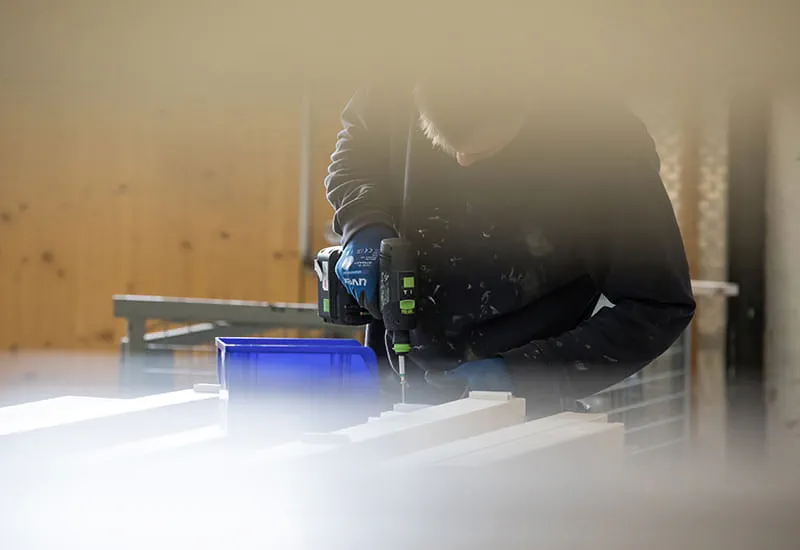
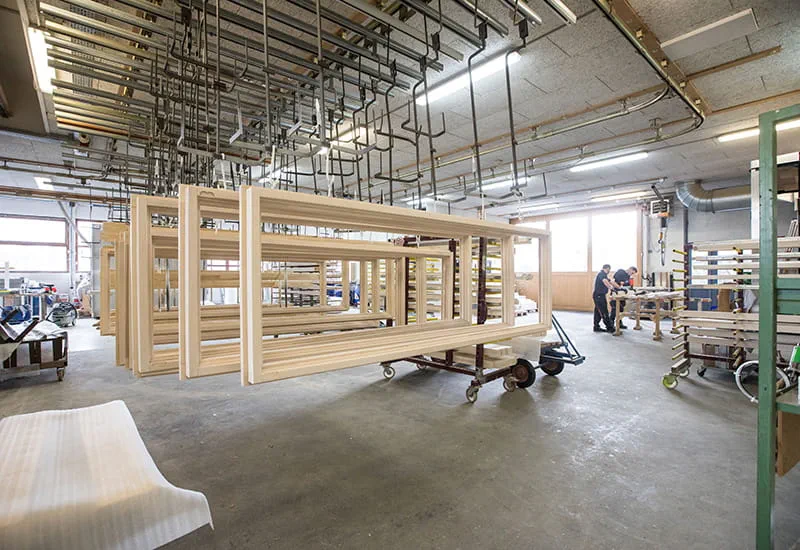
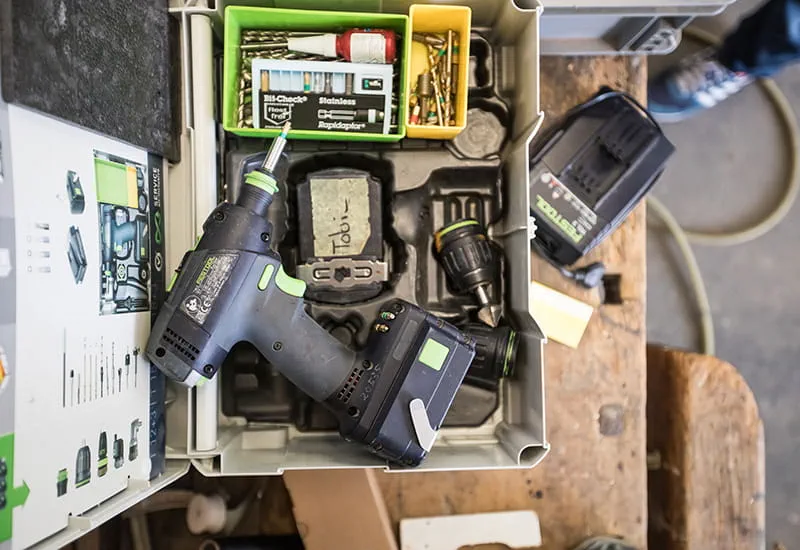
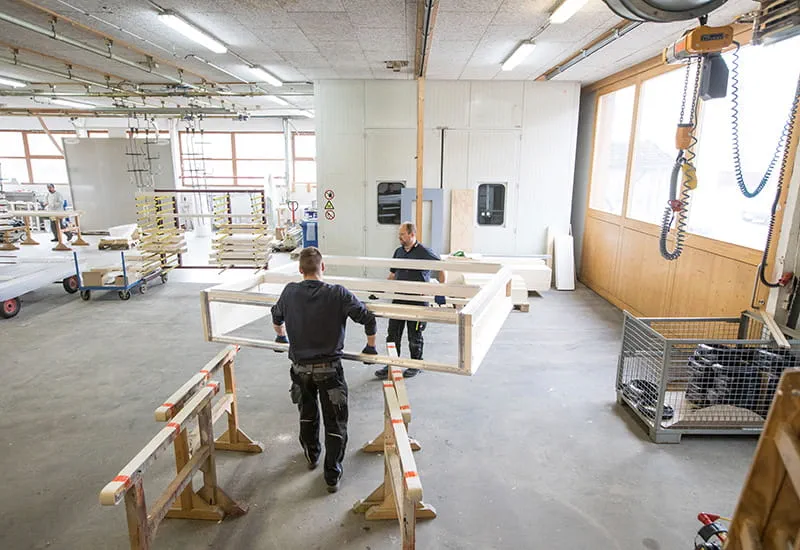
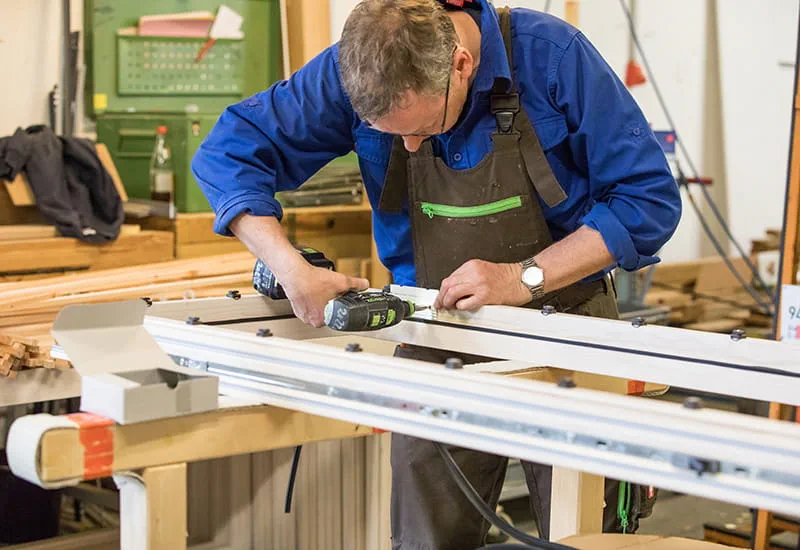
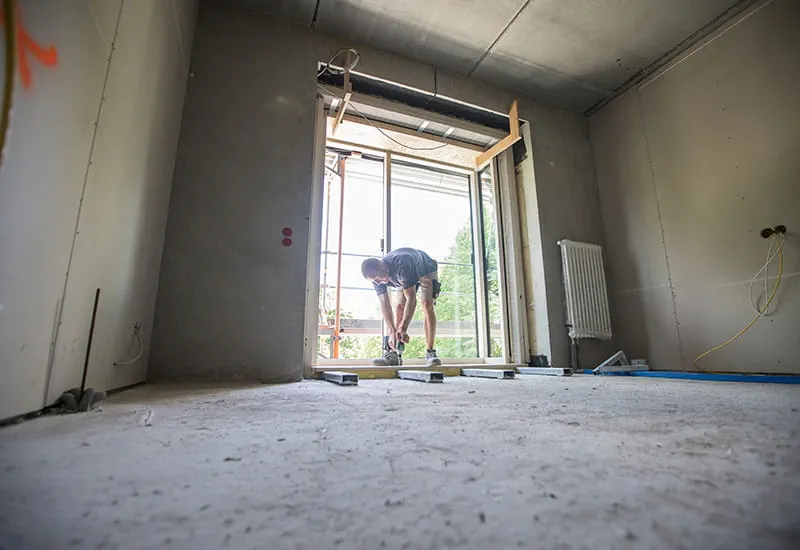
1 / 1
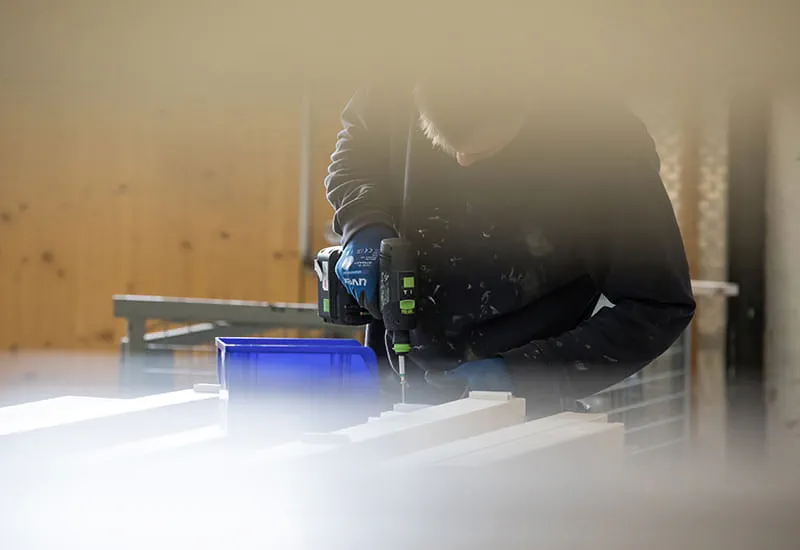
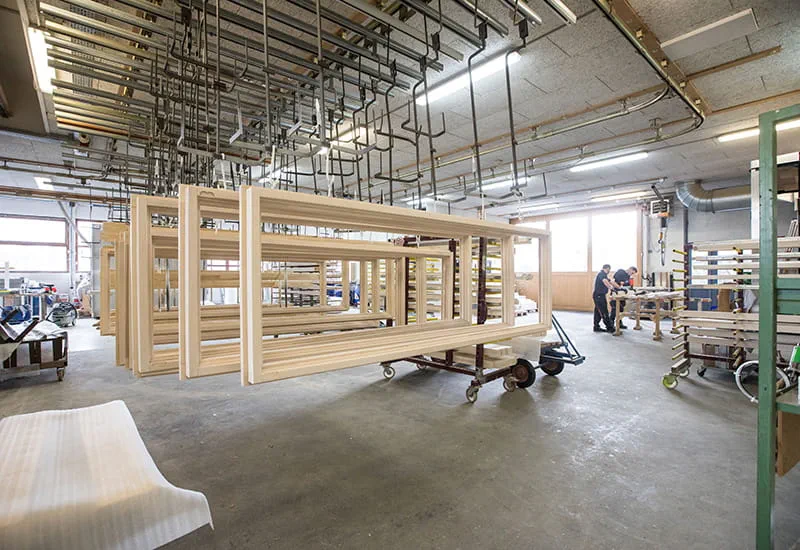
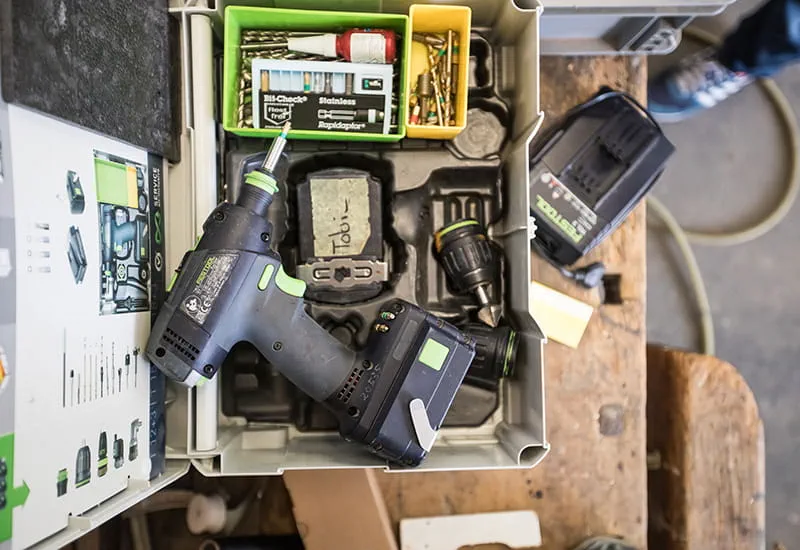
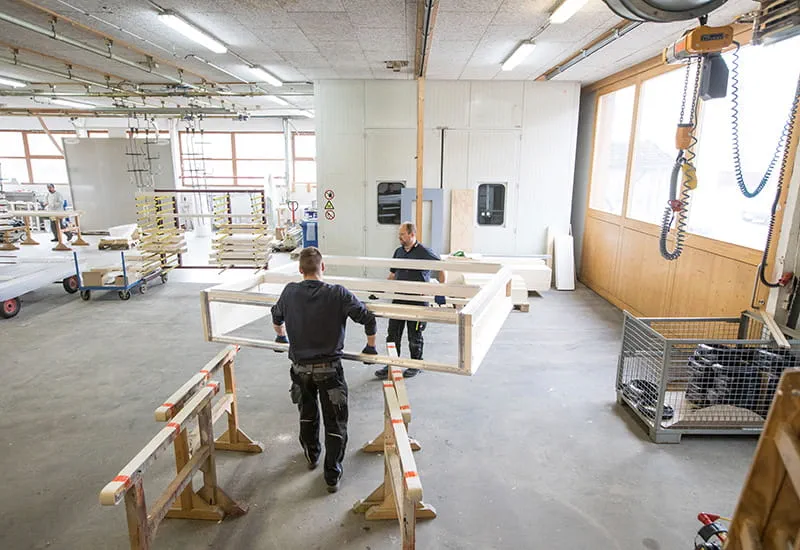
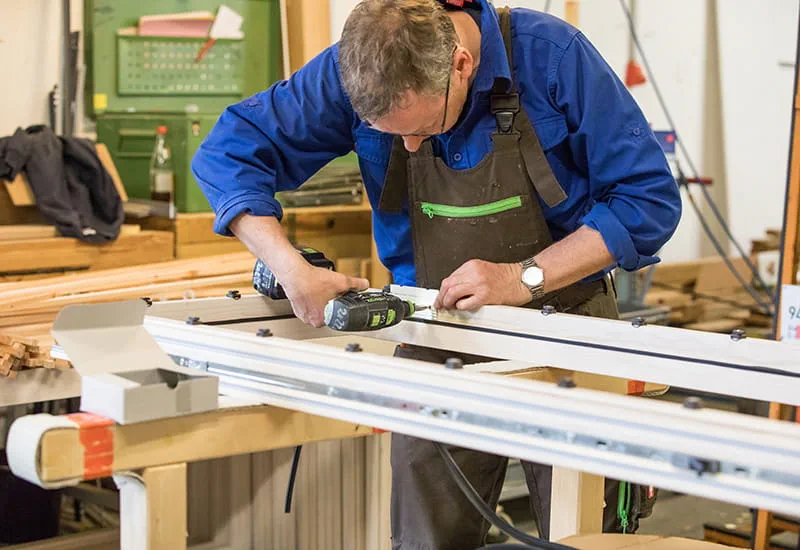
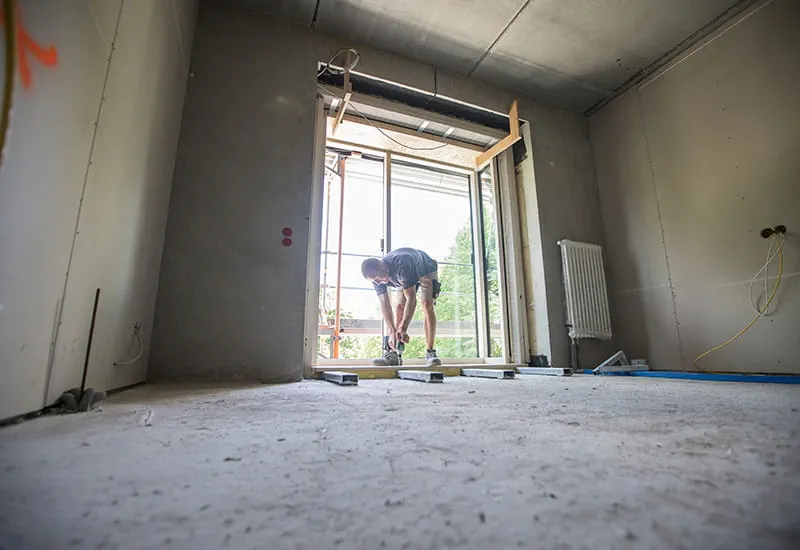